AI assistant for heavy machinery control to support wellbeing – preventing stress and collisions
Press release from the University of Oulu
Real-time simulation is being harnessed to support the well-being of heavy machinery and pilots in a new research project by the University of Oulu, LUT University and Aalto University. Simplifying machine operation reduces operator stress and mechanical stress on machinery.
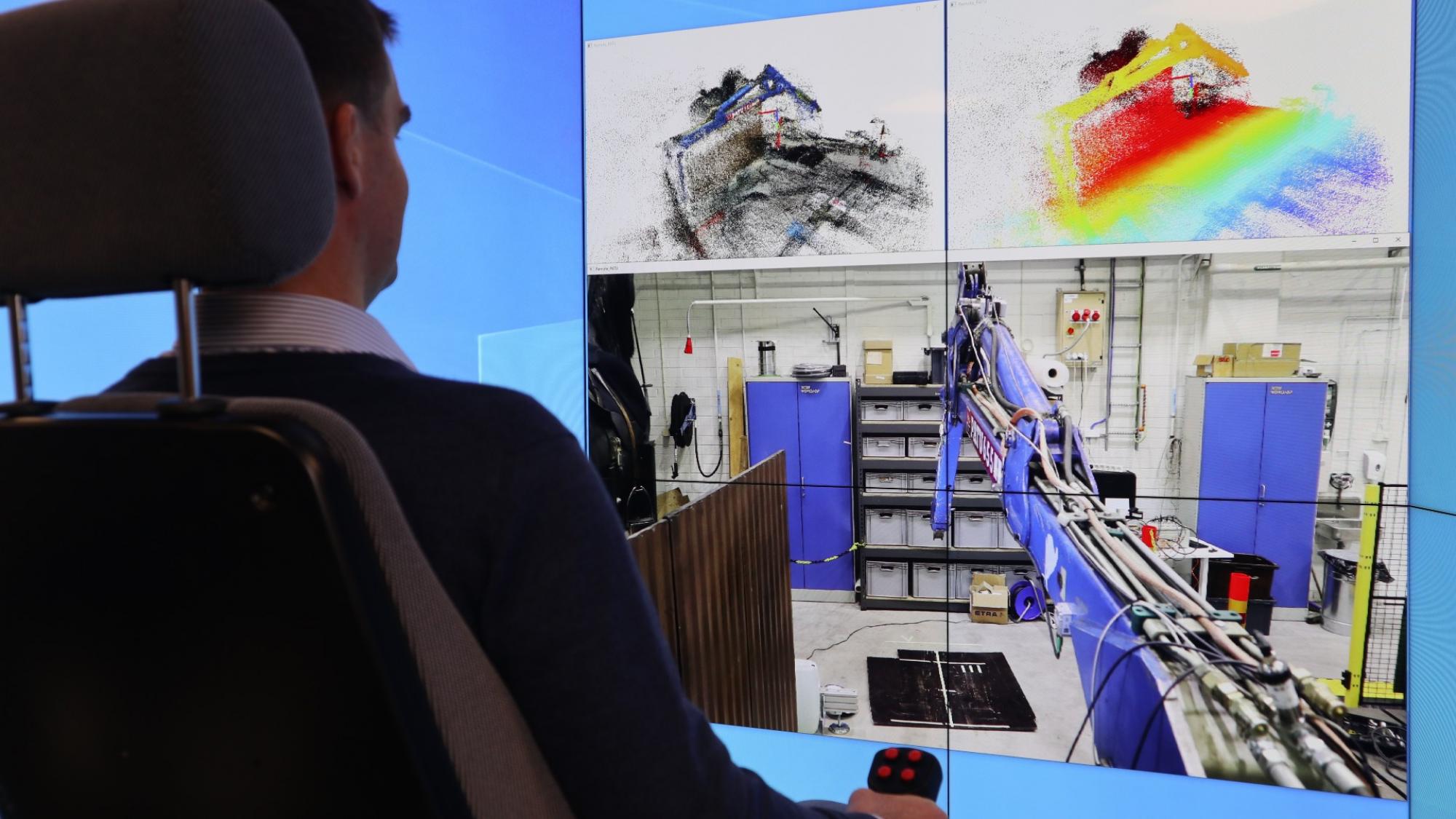
The industry’s digital revolution affects how heavy machine manufacturing companies produce services and develop their operations. In the Finnish industry, mechanical engineering is one industry that is strongly affected by the digital revolution, which further creates a need for software and know-how development.
At the national level, high-tech products are often highly customized to meet customer needs and are used globally. Software development for customized machines requires machine-specific information and an understanding of their behavior to make the software work efficiently and as planned. Simulation techniques based on real-time simulation and artificial intelligence techniques enable the development of intelligent features, for example, for heavy machine applications already in the planning phase, which can be used to influence productivity, efficiency, and the operator’s well-being.
“In modern simulations, it is possible to accurately model not only the machine, but also the environment, so there is great potential to use these models in the development of new features of the machines,” says Sandvik Mining and Construction Oy’s Engineering Manager Arto Vento.
In the Santtu joint research project the focus is on the development of support systems for operators of work machines and heavy industry machines in strong cooperation with the Finnish industry. The goal is to simplify the control and use of machines with the help of semi-autonomous operator assistance systems. This can be used to reduce the operator’s cognitive load and the stress on the device, so that the machines’ lifespan, usability, and productivity can be improved.
Combining physics-based (real-time) simulation, digital twins, and artificial intelligence techniques makes it possible to create semi-automatic systems. The objective is to develop a model-based, artificial intelligence-assisted solution that offers collision prevention, strain optimization, improved accuracy, automation of work routines, and human-centered user interface design. With these, the skill requirements for efficient use of the machine are lowered, which realistically expands the target market, especially in fast-growing market areas.
“Simulation-based, especially with the help of real-time dynamics calculation, it is possible to develop software and features that are customized for each machine, enabling the energy-efficient use of machines and improving the productivity of the equipment,” says Emil Kurvinen, professor of machine design at the University of Oulu.
Santtu research project
The project involves Sandvik Mining and Construction Oy, Raute Oyj, Ponsse Oyj, and Mantsinen Oy, as well as three universities LUT University, Aalto University and University of Oulu. In addition, the monitoring companies are Mevea Oy and GIM Robotics Oy, as well as Sustainable Industry X (SIX) and FIMA Ry, and the whole project is connected to the Sandvik Shift’25 Business Finland Veturi program. The project is funded by the Business Finland co-innovation instrument and is part of the Sustainable Manufacturing program. The public research project lasts two years from 1st of April 2022 to 31st of March 2024.
- WHAT? Simplification of the control and operation of the machine through semiautonomous operator assistance systems
- WHY? Decrease both the cognitive stress of the operator and the mechanical stress to the machine to increase the lifetime and usability of the machinery
- HOW? Combining beyond state-of-the-art physics-based simulation models, digital twins and artificial intelligence techniques to reach higher levels of autonomous features
- RESULTS Model-based AI assistant that provides collision and stress prevention, improved accuracy, automation of experiential routines and human-centric HMI design
The project is implemented as a collaboration between three universities:
- In the mechanical and vehicle engineering research group of the material and mechanical engineering research unit of the University of Oulu, led by Emil Kurvinen, professor of mechanical engineering
- On LUT University’s interdisciplinary SIM platform. Included are the following research groups: Lea Hannola’s innovation management, Aki Mikkola’s virtual design, Paavo Ritala’s strategy and innovation, Minna Saunila’s performance management, and Heikki Handroos’ intelligent machines. See more: moresim.fi
- At Aalto University’s School of Electrical Engineering, in the Intelligent Robotics group, Led by prof. Ville Kyrki
Originally published on 16 January.
Announcements are published as a service to readers. The sender is responsible for all content.
Announcements for publication can be submitted to pr***********@ar**************.com.